🎯 سیستم خنککننده در قالب تزریق پلاستیک (Cooling System in Injection Molds)
مقدمه
فرآیند تزریق پلاستیک یکی از رایجترین روشها برای تولید قطعات پلاستیکی در صنایع مختلف است. این فرآیند شامل مراحل مختلفی از جمله ذوب ماده پلاستیکی، تزریق آن به قالب، و در نهایت خنککاری است. یکی از مهمترین بخشها در طراحی قالبهای تزریق پلاستیک، سیستم خنککننده است که نقش حیاتی در کیفیت قطعه نهایی، زمان تولید، و عملکرد قالب ایفا میکند. خنککاری نامناسب میتواند به مشکلاتی مانند انقباض غیر یکنواخت، تاببرداشتگی (Warpage) یا حتی خرابی قالب منجر شود. طراحی بهینه سیستم خنککننده میتواند به کاهش زمان سیکل تولید و بهبود کیفیت قطعه کمک کند.
عملکرد سیستم خنککننده
در فرآیند قالب تزریق پلاستیک، قالب باید به سرعت حرارت را از ماده پلاستیکی مذاب جذب کرده و آن را به یک دمای مناسب برای خروج از قالب برساند. سیستم خنککننده شامل مجموعهای از کانالهای خنککننده است که بهطور استراتژیک در داخل قالب قرار میگیرند. این کانالها معمولاً با سیال خنککننده (معمولاً آب) پر میشوند تا دمای قالب و قطعه تولیدی را کاهش دهند. طراحی مناسب این کانالها نیازمند توجه به نکات مختلف است که در اینجا به بررسی آنها میپردازیم.
📌 تأثیر جنس ماده پلاستیکی بر خنککاری
نوع پلاستیک استفادهشده تأثیر زیادی بر فرآیند خنککاری دارد. مواد مختلف پلاستیکی خصوصیات حرارتی متفاوتی دارند که میتواند نیاز به سیستم خنککننده متفاوتی ایجاد کند. برای مثال:
نوع ماده | ویژگی حرارتی | تأثیر بر طراحی خنککاری |
---|---|---|
ABS | رسانایی حرارتی پایین | نیاز به خنککاری یکنواخت و گستردهتر |
پلیپروپیلن (PP) | انقباض بالا | کانالها باید نزدیکتر به حفره طراحی شوند |
پلیآمید (Nylon) پرشده با الیاف | گرمای زیاد و نرخ سردشدن بالا | نیاز به دقت بیشتر در کنترل دما |
پلیکربنات (PC) یا PSU | حساس به تغییرات حرارتی | خنککاری ملایم و بدون شوک حرارتی ضروری است |
✅ نکته: توجه به ویژگیهای حرارتی ماده، تضمین میکند که سیستم خنککننده به بهترین شکل ممکن عمل کند و از بروز مشکلاتی مانند انقباض یا تاببرداشتگی جلوگیری شود.
📌 نقش طراحی کلی قالب تزریق پلاستیک در عملکرد خنککاری
طراحی قالب بهطور کلی و بهویژه طراحی سیستم خنککننده، تأثیر زیادی بر کیفیت تولید و سرعت چرخه تزریق دارد. در طراحی قالب، باید به موارد زیر توجه ویژهای داشت:
فاکتور طراحی | تأثیر بر سیستم خنککننده | نکات مهم طراحی |
---|---|---|
توزیع کانالهای خنککننده | توزیع یکنواخت دما و کاهش انقباض غیر یکنواخت | کانالها باید بهطور استراتژیک در قالب قرار گیرند |
شکل قالب | نواحی با ضخامت دیوارههای زیاد نیاز به سیستم خنککننده پیشرفتهتر دارند | دقت در طراحی کانالها به ویژه در نواحی پیچیده |
کانالهای مارپیچی و انحنادار | بهبود انتقال حرارت و جلوگیری از نقاط داغ (Hot Spots) | برای کنترل بهتر دما و بهبود خنککاری در نواحی خاص |
طراحی قالب چندحفرهای | تعادل دمایی در قالبهای چندحفرهای برای یکنواختی تولید | طراحی کانالها باید بهگونهای باشد که دما در تمام حفرهها یکسان باشد |
📌 فرمول محاسبه قطر کانال خنککننده
فرمول زیر برای محاسبه قطر کانالهای خنککننده در قالبهای تزریق پلاستیک استفاده میشود:
D=4QπvD = \sqrt{\frac{4Q}{\pi v}}D=πv4Q
DDD: قطر کانال (متر)
QQQ: دبی جریان آب (m³/s)
vvv: سرعت جریان آب (m/s)
توصیه میشود که سرعت جریان آب بین 0.5 تا 1.5 متر بر ثانیه باشد تا انتقال حرارت به بهترین نحو ممکن انجام شود.
📌 انتخاب قطر کانال خنککننده بر اساس ابعاد قالب
برای طراحی بهینه سیستم خنککننده در قالبهای تزریق پلاستیک، قطر کانالها باید متناسب با ضخامت دیواره قالب انتخاب شود. جدول زیر کمک میکند تا بتوانید قطر مناسب کانالهای خنککننده را بر اساس ابعاد قالب تعیین کنید:
ضخامت دیواره قالب (mm) | قطر کانال خنککننده (mm) | توضیحات |
---|---|---|
1.5 – 3 | 3 – 4 | برای قالبهای با دیوارههای نازک، قطر کانالها کوچکتر انتخاب میشود. |
3 – 6 | 4 – 6 | برای قالبهای با ضخامت متوسط، قطر کانالها به میزان متوسط میرسد. |
6 – 10 | 6 – 8 | برای قالبهای با ضخامت زیاد، قطر کانالها باید بزرگتر انتخاب شود تا انتقال حرارت بهینه انجام گیرد. |
10 – 20 | 8 – 12 | برای قالبهای صنعتی و بزرگتر، استفاده از کانالهای با قطر بزرگتر توصیه میشود. |
20+ | 12 – 16 | در قالبهای با ضخامت دیواره بیشتر، قطر کانالهای خنککننده باید بزرگتر باشد تا کارایی سیستم بهینه شود. |
نکات مهم در انتخاب قطر کانال خنککننده:
جریان سیال: برای انتقال حرارت بهینه، سرعت جریان سیال (آب یا سایر مایعات خنککننده) باید در محدوده معقول باشد. معمولاً سرعت جریان بین 0.5 تا 1.5 متر بر ثانیه ایدهآل است.
افت فشار: قطر بیشتر کانال میتواند باعث کاهش افت فشار شود، اما هزینه و پیچیدگی ساخت قالب افزایش مییابد.
زمان سیکل تولید: افزایش قطر کانال میتواند زمان خنککاری را کاهش دهد، اما باید از ایجاد تداخل با سایر اجزای قالب جلوگیری کرد.
طراحی بهینه: در قالبهای پیچیده یا قالبهایی که دارای حفرههای زیاد هستند، انتخاب قطر کانالها باید بهگونهای باشد که توزیع حرارت یکنواخت باشد و از مشکلاتی مانند تاببرداشتگی جلوگیری کند.
مثال از کاربرد جدول انتخاب قطر کانال:
اگر قالب شما ضخامت دیوارهای بین 6 تا 10 میلیمتر داشته باشد، طبق جدول فوق، انتخاب قطر کانال بین 6 تا 8 میلیمتر برای قالب شما مناسب خواهد بود. این انتخاب میتواند به طور موثر در کاهش زمان سیکل تولید و بهبود کیفیت قطعه نهایی کمک کند.
این جدول به عنوان یک راهنما میتواند در طراحی اولیه سیستم خنککننده در قالبهای تزریق پلاستیک کمککننده باشد. امیدوارم این جدول مفید واقع شود. اگر نیاز به جداول دیگری یا اطلاعات بیشتری دارید، خوشحال میشم کمک کنم!
📌 تحلیل و طراحی در نرمافزار Moldflow
برای انجام تحلیل دقیقتر سیستم خنککننده در قالبهای تزریق پلاستیک، استفاده از ابزارهای نرمافزاری پیشرفته مانند Moldflow Insight میتواند به مهندسان کمک کند. مراحل طراحی در این نرمافزار شامل:
مرحله | توضیحات |
---|---|
وارد کردن مدل قالب | مدل سهبعدی قالب باید به صورت دقیق وارد نرمافزار شود. |
تعریف هندسه قالب و مشخصات پلاستیک | اطلاعات دقیق از مواد پلاستیکی و ویژگیهای حرارتی آنها وارد میشود. |
مدلسازی سیستم خنککننده | باید کانالهای خنککننده طراحی شده و به نرمافزار وارد شوند. |
تحلیل توزیع حرارت | نرمافزار به تحلیل توزیع دمای قالب و قطعه پرداخته و نقاط بحرانی را شناسایی میکند. |
بهینهسازی سیستم خنککننده | طراحی کانالهای خنککننده بهینه میشود تا زمان سیکل تولید کاهش یابد و کیفیت قطعه نهایی ارتقاء یابد. |
📌 نکات کلیدی در طراحی کانالهای خنککننده:
موقعیت کانالها: کانالها باید به نحوی در قالب قرار گیرند که دمای قطعه بهطور یکنواخت کاهش یابد.
کنترل فشار و سرعت جریان: کنترل دقیق فشار و سرعت جریان آب در کانالهای خنککننده به بهبود کارایی سیستم کمک میکند.
طراحی کانالهای پیچیده: در صورت نیاز به خنککاری دقیق در نواحی خاص قالب، از طراحی کانالهای مارپیچی یا انحنادار استفاده میشود.
نتیجهگیری
در نهایت، طراحی صحیح سیستم خنککننده در قالب تزریق پلاستیک نهتنها به کاهش زمان تولید و بهبود کیفیت قطعه کمک میکند، بلکه باعث افزایش طول عمر قالب و کاهش هزینههای تولید میشود. با استفاده از ابزارهایی مانند Moldflow و با در نظر گرفتن نکات فنی مهم، میتوان سیستم خنککننده بهینه را طراحی کرد که برای هر نوع پلاستیک و قالب خاص مناسب باشد.
1. نوع سیال خنککننده
انتخاب نوع سیال خنککننده میتواند تأثیر زیادی بر عملکرد سیستم خنککننده داشته باشد. علاوه بر آب، از سیالاتی مانند روغنهای معدنی یا سیالات ویژه با خواص حرارتی بالا استفاده میشود.
نکات مهم:
آب: رایجترین سیال است، اما باید تصفیه شود تا از ایجاد رسوب و گرفتگی در کانالها جلوگیری شود.
روغنهای خاص: در دماهای بالاتر و در شرایطی که نیاز به انتقال حرارت بیشتری باشد، میتوان از روغنهای ویژه استفاده کرد.
سیالات با هدایت حرارتی بالا: برای کاربردهای خاص، ممکن است نیاز به سیالات خنککننده با هدایت حرارتی بالا باشد.
2. جریان داخل کانالها
برای افزایش کارایی سیستم خنککننده، باید توجه ویژهای به نوع جریان داخل کانالهای خنککننده داشته باشیم. جریان سیال میتواند بهصورت جریان لایهای (Laminar) یا جریان آشفته (Turbulent) باشد که هرکدام تأثیرات مختلفی بر انتقال حرارت دارند.
نکات مهم:
جریان لایهای: در این حالت، انتقال حرارت به صورت محدود است و معمولاً در کانالهای باریک با دبی پایین مشاهده میشود.
جریان آشفته: باعث بهبود انتقال حرارت میشود و بیشتر در کانالهای بزرگتر با سرعت جریان بالاتر اتفاق میافتد. استفاده از این نوع جریان میتواند برای قالبهای با دماهای بالاتر مناسب باشد.
3. تأثیر سرعت جریان سیال
سرعت جریان سیال در کانالهای خنککننده نقش مهمی در کاهش زمان سرد شدن قالب و افزایش کیفیت قطعه دارد. در صورتی که سرعت جریان کمتر از حد بهینه باشد، انتقال حرارت به کندی انجام میشود. از طرف دیگر، سرعتهای بسیار بالا میتوانند باعث ایجاد افت فشار و حتی آسیب به سیستم شوند.
نکات مهم:
سرعت جریان باید بهگونهای تنظیم شود که بیشترین کارایی انتقال حرارت را داشته باشد.
بررسی افت فشار در کانالها برای اطمینان از عدم وجود مشکلات در سیستم بسیار ضروری است.
4. کانالهای خنککننده متغیر (Variable Cooling Channels)
یکی از نوآوریهای جدید در طراحی قالبهای تزریق پلاستیک، استفاده از کانالهای خنککننده متغیر است که میتوانند به صورت دینامیک تغییر اندازه دهند و دمای قالب را در نواحی مختلف بهینه کنند. این نوع سیستمها معمولاً با استفاده از تکنولوژیهای مدرن مانند سیستمهای هیدرولیکی یا پنوماتیکی به کار گرفته میشوند.
مزایای این نوع سیستمها:
بهینهسازی توزیع دما در طول فرآیند تزریق.
کاهش زمان سیکل تولید.
پیشگیری از مشکلات تاببرداشتگی در قطعات.
5. خنککاری بهینه با استفاده از تکنولوژیهای 3D Printing
در حال حاضر، فناوری چاپ سهبعدی (3D Printing) در طراحی قالبها و سیستمهای خنککننده استفاده میشود. با استفاده از این تکنولوژی، میتوان کانالهای خنککننده پیچیده و با ابعاد دقیقتری طراحی کرد که بهبود کارایی سیستم خنککننده را به همراه دارد.
مزایای استفاده از چاپ سهبعدی در طراحی کانالهای خنککننده:
امکان طراحی کانالهای خنککننده با اشکال پیچیده و خاص که قبلاً قابل انجام نبودهاند.
امکان تولید قالبهای سفارشی با هزینه کمتر در مقایسه با روشهای سنتی.
بهبود توزیع حرارت و کاهش زمان سرد شدن.
6. تأثیر مواد قالب بر سیستم خنککننده
جنس و ساختار قالب تزریق پلاستیک نیز تأثیر مستقیمی بر عملکرد سیستم خنککننده دارد. به عنوان مثال، آلیاژهای فلزی خاص مانند H13 یا P20 معمولاً برای قالبهای تزریق پلاستیک استفاده میشوند و هرکدام خصوصیات حرارتی متفاوتی دارند. برای این قالبها ممکن است نیاز به کانالهای خنککننده متفاوت با فاصلهها و قطرهای خاص باشد.
7. سیستمهای خنککننده اضافی
در برخی از موارد، علاوه بر سیستم خنککننده اصلی قالب، میتوان از سیستمهای خنککننده اضافی استفاده کرد که از طریق سیستمهای پشتیبان دمای قطعه را کنترل کنند. این سیستمها میتوانند برای قطعات با نیازهای خاص (مثل مواد حساس به دما) مورد استفاده قرار گیرند.
8. محاسبه و بهینهسازی زمان سیکل
زمان سیکل در فرآیند تزریق پلاستیک نقش بسیار مهمی دارد و سیستم خنککننده یکی از عوامل کلیدی در کاهش آن است. بهینهسازی زمان خنککاری به کمک طراحی مناسب کانالها، انتخاب صحیح سیال خنککننده، و استفاده از سیستمهای پیشرفته میتواند زمان کلی تولید را به طور قابل توجهی کاهش دهد.
9. تحلیل تغییرات دما در طول زمان
برای بهبود عملکرد سیستم خنککننده، تحلیل دقیق تغییرات دما در قالب و قطعه ضروری است. سیستمهای نظارت دمایی پیشرفته میتوانند به شبیهسازی دقیق تغییرات دمای قالب در طول فرآیند کمک کنند و از بروز مشکلاتی مانند دمای نامناسب در حفرهها جلوگیری نمایند.
10. توجه به پایداری و دوام سیستم خنککننده
در طراحی سیستم خنککننده، پایداری و دوام سیستم بسیار اهمیت دارد. سیستم خنککننده باید مقاوم در برابر فشار بالا، دمای بالا و رسوبات باشد تا طول عمر قالب و کارایی سیستم حفظ شود.
نتیجهگیری نهایی
طراحی بهینه سیستم خنککننده در قالب تزریق پلاستیک بخش مهمی از فرآیند تولید قطعات با کیفیت و کاهش زمان سیکل تولید است. با توجه به جنس پلاستیک، طراحی قالب، انتخاب مناسب سیال خنککننده، و استفاده از ابزارهای پیشرفته مانند نرمافزار Moldflow، میتوان سیستمهای خنککنندهای ایجاد کرد که کارایی بالا و هزینه تولید پایینتری داشته باشند. همچنین، با توجه به پیشرفتهای تکنولوژی مانند چاپ سهبعدی و سیستمهای خنککننده متغیر، میتوان به طراحیهای پیچیدهتر و بهینهتری دست یافت که باعث بهبود کیفیت و کاهش مشکلات تولید میشود.
1. استفاده از فناوریهای نوین در طراحی قالب
امروزه با استفاده از فناوریهای پیشرفته مانند شبیهسازی و تحلیل عددی (Computational Fluid Dynamics – CFD) و چاپ سهبعدی، میتوان سیستمهای خنککننده دقیقتری طراحی کرد. این تکنولوژیها به طراحی دقیق کانالهای خنککننده و پیشبینی نحوه جریان سیال کمک میکنند تا بیشترین کارایی را از سیستم خنککننده بدست آوریم.
نکات مهم:
استفاده از تحلیل جریان سیال در نرمافزارهای CFD میتواند به پیشبینی توزیع دما و فشار کمک کند.
چاپ سهبعدی امکان طراحی کانالهای پیچیده و بهینهسازی سریعتر قالبها را فراهم میآورد.
2. خنککاری در قالبهای چندحفرهای
در قالبهای چندحفرهای، سیستم خنککننده باید بهگونهای طراحی شود که انتقال حرارت در تمام حفرهها بهصورت یکنواخت انجام گیرد. این کار میتواند به کاهش زمان سیکل و بهبود کیفیت قطعات کمک کند. یکی از چالشهای طراحی این قالبها، کنترل دما در تمام حفرهها است.
نکات طراحی:
برای بهینهسازی سیستم خنککننده در قالبهای چندحفرهای، طراحی کانالها باید به گونهای باشد که دما در همه حفرهها یکسان باشد.
استفاده از کانالهای مارپیچی یا کانالهای چند مرحلهای برای انتقال حرارت یکنواختتر میتواند بسیار مؤثر باشد.
3. ملاحظات مربوط به تاببرداشتگی (Warpage)
یکی از مشکلات رایج در تولید قطعات پلاستیکی، تاببرداشتگی (Warpage) است که به علت انقباض غیر یکنواخت در فرآیند خنککاری به وجود میآید. این مسئله بهویژه زمانی مهم میشود که قطعه دارای ویژگیهای پیچیده و دیوارههای با ضخامتهای متفاوت باشد.
راهکارها برای جلوگیری از تاببرداشتگی:
طراحی کانالهای خنککننده باید به گونهای باشد که انقباض در تمامی نواحی قالب یکنواخت باشد.
استفاده از سیستمهای خنککننده دقیق و بهینهسازی توزیع دما میتواند از بروز تاببرداشتگی جلوگیری کند.
4. زمان سرد شدن و تأثیر آن بر کیفیت قطعه
زمان سرد شدن قطعه پلاستیکی مستقیماً به زمان خنککاری بستگی دارد. هر چه زمان سرد شدن کمتر باشد، تعداد قطعات تولیدی بیشتر و هزینه تولید کمتر خواهد بود. طراحی دقیق سیستم خنککننده باعث کاهش زمان سرد شدن میشود.
نکات مهم:
در قالبهای پیچیده، باید از کانالهای خنککننده اضافی برای کاهش زمان سرد شدن استفاده کرد.
استفاده از سیالات خنککننده با هدایت حرارتی بالا میتواند به سرعت بخشیدن به فرآیند سرد شدن کمک کند.
5. تأثیر ضخامت دیواره بر طراحی سیستم خنککننده
ضخامت دیواره قالب یکی از عوامل مؤثر در طراحی سیستم خنککننده است. به طور کلی، هر چه ضخامت دیواره بیشتر باشد، نیاز به سیستم خنککننده پیچیدهتری خواهید داشت.
نکات طراحی:
در قالبهای با دیوارههای ضخیم، طراحی کانالهای خنککننده بزرگتر و نزدیکتر به حفرهها ضروری است.
برای جلوگیری از افزایش زمان تولید در قالبهای با دیوارههای ضخیم، استفاده از سیالات خنککننده با سرعت جریان بالا توصیه میشود.
6. خنککاری در فرآیندهای ویژه مانند قالبگیری تزریقی با گاز (Gas-assisted injection molding)
در فرآیندهای ویژه مانند قالبگیری تزریقی با گاز، به دلیل تولید حبابهای گازی در داخل قطعه، سیستم خنککننده باید بهگونهای طراحی شود که حرارت را سریعتر از قالب خارج کند.
چالشها:
در این فرآیندها، ممکن است نیاز به طراحی خاصی برای کانالهای خنککننده باشد تا از شکستن یا خرابی قطعه جلوگیری شود.
استفاده از سیستمهای خنککننده پرفشار برای ایجاد دمای یکنواخت و جلوگیری از حفرههای هوا ضروری است.
7. نگهداری و تعمیرات سیستم خنککننده
یکی از جنبههای حیاتی سیستم خنککننده در قالبهای تزریق پلاستیک، نیاز به نگهداری منظم و تعمیرات به موقع است. رسوبات ناشی از سیالات خنککننده، آلودگی یا خرابی کانالها میتواند عملکرد سیستم را به شدت کاهش دهد.
اقدامات پیشگیرانه:
شستشو و تصفیه سیالات خنککننده بهطور منظم برای جلوگیری از رسوبات و گرفتگی کانالها.
بررسی دورهای پمپها و تجهیزات جانبی برای اطمینان از عملکرد صحیح.
8. مطالعه و بهینهسازی سیستمهای خنککننده با دادههای واقعی
جمعآوری دادههای واقعی از سیستمهای خنککننده موجود میتواند به بهینهسازی بیشتر کمک کند. استفاده از سیستمهای نظارتی دما و حسگرهای فشار به شما این امکان را میدهد تا اطلاعات دقیقتری از عملکرد سیستم داشته باشید و مشکلات را بهسرعت شناسایی کنید.
مزایا:
بهینهسازی کارایی سیستم در زمان واقعی.
شناسایی و رفع مشکلات قبل از بروز خرابیهای بزرگ.
9. مدیریت هزینهها و انتخاب مواد
انتخاب صحیح مواد برای سیستمهای خنککننده میتواند تأثیر زیادی بر هزینههای تولید و عملکرد قالب داشته باشد. استفاده از مواد با ویژگیهای حرارتی بالا مانند مس یا آلومینیوم برای ساخت قالبها و کانالهای خنککننده ممکن است هزینههای اولیه را افزایش دهد، اما در بلندمدت میتواند موجب کاهش هزینههای تولید و بهبود کیفیت قطعات شود.
نکات هزینهای:
ارزیابی دقیق هزینه و عملکرد در انتخاب مواد قالب و سیال خنککننده.
بهینهسازی طرح به گونهای که هزینهها و زمان تولید کاهش یابد.
نتیجهگیری نهایی:
با استفاده از راهکارهای نوآورانه، طراحی بهینه کانالهای خنککننده و توجه به جزئیات دقیق در فرآیند تزریق پلاستیک، میتوان به عملکرد بهتری در تولید قطعات با کیفیت و کاهش زمان تولید دست یافت. نکات و تکنیکهای مختلفی که در این مقاله مورد بررسی قرار گرفت، میتواند به مهندسان کمک کند تا سیستم خنککنندهای با کارایی بالا، عمر طولانی و هزینه کم طراحی کنند.
🎯 سیستم خنککننده در قالب تزریق پلاستیک (Cooling System in Injection Molds)
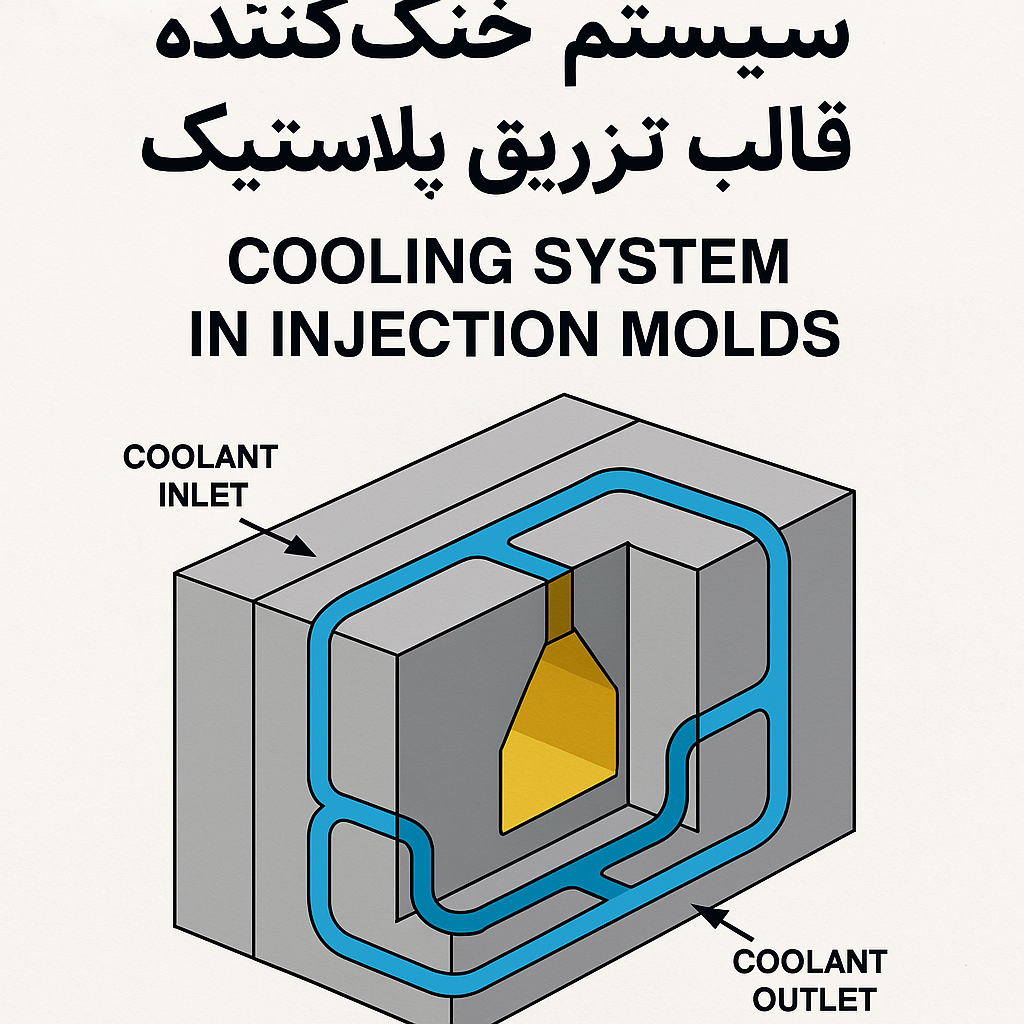
Related Posts
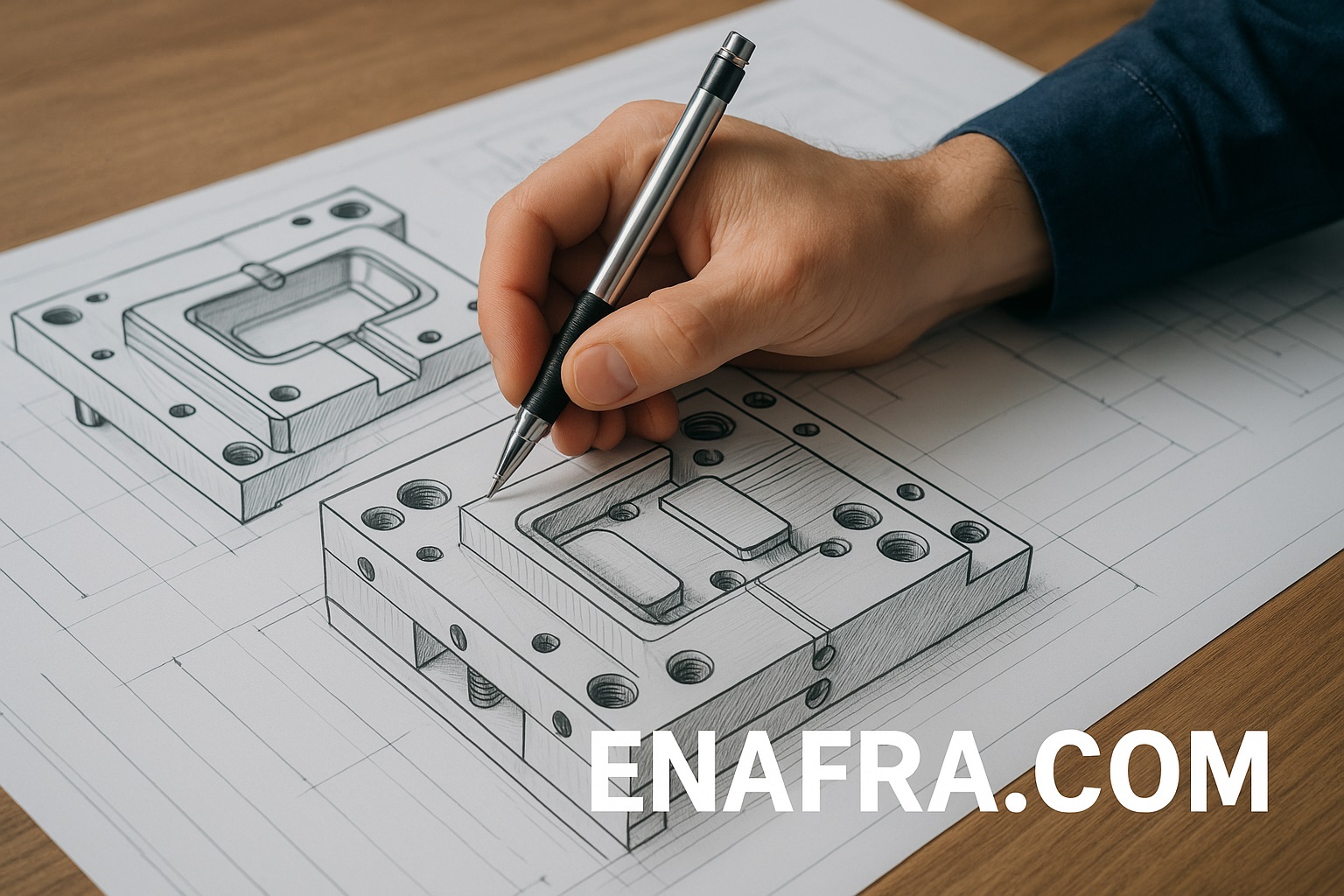
قیمت قالب تزریق پلاستیک در سال 1404 + جدول قیمتها
قالب تزریق پلاستیک یکی از ابزارهای کلیدی در تولید قطعات پلاستیکی است که قیمت آن تحت تأثیر عوامل متعددی مانند جنس قالب، پیچیدگی طراحی، تعداد کویتهها و تیراژ تولید قرار دارد. در سال ۱۴۰۳ با توجه به تغییرات بازار و فناوری، اطلاع دقیق از قیمت قالبها برای تولیدکنندگان اهمیت ویژهای یافته است. این مقاله به بررسی جامع قیمتهای بهروز قالب تزریق پلاستیک، عوامل مؤثر بر هزینهها، نکات کاربردی در انتخاب قالب مناسب و پاسخ به سوالات متداول میپردازد تا به شما در تصمیمگیری بهتر کمک کند.
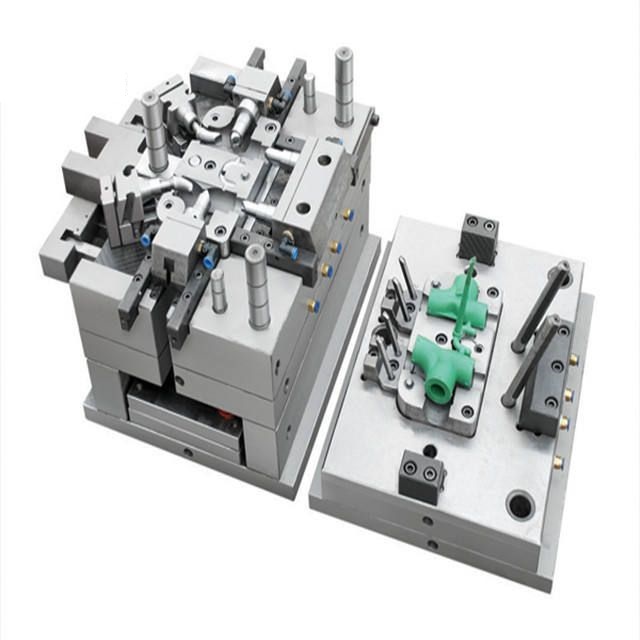
هزینه ساخت قالب تزریق پلاستیک
در این مقاله جامع، با عوامل تاثیرگذار بر هزینه ساخت قالب تزریق پلاستیک آشنا میشوید. از ابعاد و پیچیدگی قطعه گرفته تا نوع فولاد و تعداد حفرهها، همه فاکتورهای موثر بر قیمت بررسی شدهاند. همچنین جدول قیمت تقریبی، نمونهکارهای دفتر مهندسی افرا و مراحل همکاری برای ساخت قالب ارائه شده است. در نهایت، پاسخ به سوالات متداول و راههای تماس برای استعلام قیمت دقیق آورده شده است تا مسیر تصمیمگیری برای ساخت قالب برای شما آسانتر شود.
مقالهتون خیلی جامع و کاربردی بود. توضیحات در مورد انواع سیستمهای خنککننده واقعاً کمک کرد که درک بهتری از طراحی قالب پیدا کنم. ممنون بابت محتوای ارزشمندتون
سلام، بابت مقاله کاربردی تون سپاسگزارم. دید خیلی خوبی بهم داد